A field test has been undertaken to determine whether coating solar panels with RPL would have a positive effect on their energy production and greatly reduce the effort required to maintain the panels.
RPL (Repellent Protective Layer) is a self-cleaning coating. It works by creating a photocatalytic barrier which uses exposure to light to chemically break-down dirt and other contaminates. It also creates a super hydrophilic surface which aids in self-cleaning by sheeting water and carrying away dirt and contaminates.
Goals
- To measure the change in energy production when coating a solar panel with RPL.
- To measure the effectiveness of RPL in reducing debris and pollutants from gathering on the surface of the solar panels
- To reduce the required amount of cleaning cycles.
To get the most out of your solar panels, they need to be cleaned regularly. Dust, debris and pollution can greatly reduce the efficiency of the panels. This particular solar farm suffered loss of energy production from environmental pollutants and the exhaust of the food hub which deposited oily droplets and black dust. Using harsh chemicals and brushes to remove this stuck on oil and carbon could damage the solar panels, so another option was needed.
In addition, the panels were placed almost horizontally which reduces the hydrophilic self-cleaning effect of the coating, as less water will sheet off the panels. Despite this challenging scenario, we still expected RPL to provide significant improvements in energy production.
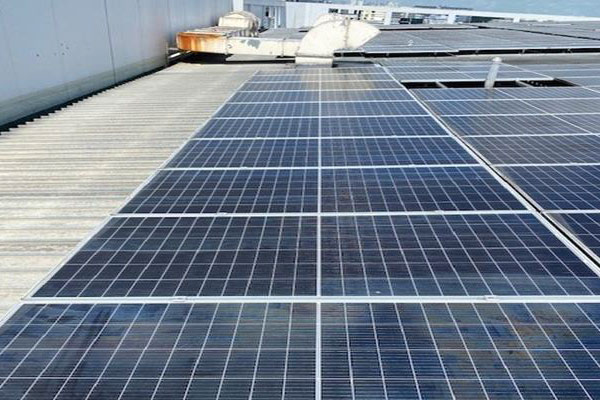
The panels were cleaned by the operator prior to coating with RPL. Both sets, the one to be coated and the control, were cleaned in an identical manner to ensure a well-controlled test. After cleaning, one layer of RPL was applied using a roller, overlapping wet-on-wet to ensure complete coverage. We used approximately 10.5ml per 10sqft.
Please Note: The optimum application method is by spray. This will give a thin, even coating that is completely invisible, whereas the roller method did leave a light white cover in areas where the application was overlapped. In this test circumstance, spraying was not possible due to the placement of the panels.
Following the coating process, the voltage and current were monitored, and data was collected every five minutes during operating hours – 7AM to 7PM. This was then converted to power in watts (W) and energy production (wH). The full test was between April 2021 to April 2022 as the timeline below outlines.
Timeline:
- May – August 2021: Normal Operation – no cleaning
- September 3, 2021: Cleaning
- September – November 2021: In use after cleaning
- November 30, 2021: Set 1 cleaned and coated with RPL, Set 2 cleaned, but not coated
- December 2021 – April 2022: In use after coating
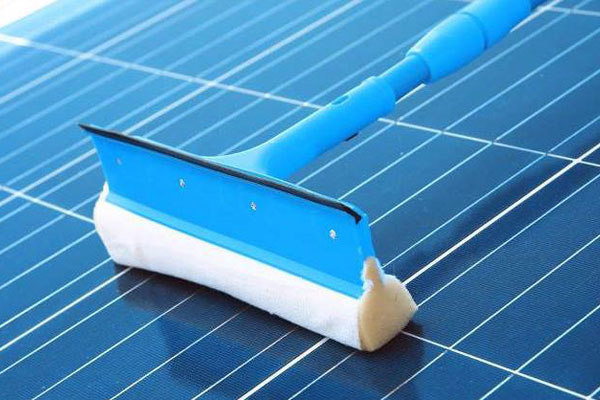
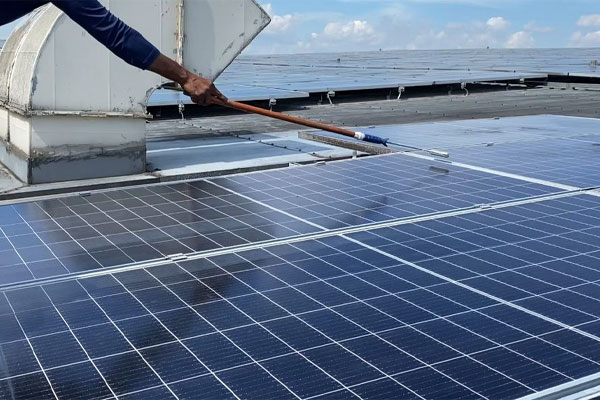